Top-Tier HVAC and AC Services at Palmdale – Quick Ease
Have you realized how essential your HVAC system is in ensuring your comfort while controlling energy bills? Here in Palmdale, Climate Control Heating, Cooling & Plumbing has led in offering top-notch HVAC and Air Conditioning services since 1987, serving more than 2500 happy customers. The NATE-certified technicians focus on delivering high-quality air conditioning repair and HVAC installation. We tailor our solutions to each household and business’s distinctive needs.
Enhancing heating and cooling may appear daunting. That’s where our services come in. We provide thorough evaluations, detailed maintenance, and efficient repairs designed to upgrade your indoor environment. Supported by a 100% satisfaction pledge and an unwavering dedication to precise workmanship, we strive to ensure your HVAC system functions without a hitch, particularly in the summer’s heat. Prevent the discomfort of abrupt malfunctions. Trust AC repair company near me to deliver reliable HVAC solutions.
Grasping HVAC Systems
An HVAC system is key to comfortable living in various climates. It handles heating, ventilation, and air conditioning. Understanding its mechanism is crucial for homeowners, especially when researching HVAC installation or evaluating heating and cooling solutions in Palmdale.
Key Elements of an HVAC Setup
An HVAC system’s effectiveness relies on the synergy of its parts. These include:
- Furnaces: They generate warmth through the combustion of fuels such as propane or natural gas.
- Air Conditioners: They reduce indoor temperatures by circulating refrigerant through internal and external coils.
- Ductwork: Essential for distributing conditioned air uniformly throughout your residence.
- Thermostats: They regulate indoor temperatures based on your settings.
- Heat Pumps: They serve dual functions by extracting heat from outside to warm or cool your home.
- Air Handlers: They distribute air around the home without adding heat, commonly combined with AC units or heat pumps.
Mechanics of HVAC Setups
HVAC setups transfer warm and cold air across your home. Normally, the furnace and AC work together to provide uninterrupted comfort. Air is heated by the furnace and propelled through ductwork by a blower. To cool, air conditioners remove heat from the interior using refrigerant to maintain optimal conditions.
Element | Role | Energy Source |
---|---|---|
Furnace | Warms the environment | Propane or natural gas |
Air Conditioner | Lowers temperature | Power |
Heat Pump | Dual functionality | Power from electricity |
Air Handler | Circulates air | Electric power |
Selecting an appropriate HVAC system in Palmdale requires factoring in local climate and your home’s needs. This knowledge helps maximize efficiency and enhance comfort.
The Value of Consistent HVAC Upkeep
Routine maintenance is crucial for ensuring that your HVAC system remains efficient and dependable. Consistent servicing improves operation and prevents costly breakdowns. Maintaining your AC in Palmdale helps lower energy expenses substantially. It ensures your system runs well throughout its life.
Advantages of Regular HVAC Servicing
Regular HVAC servicing provides many benefits:
- Energy Efficiency: Maintenance can improve efficiency by as much as 15%, potentially saving around $500 per year.
- Repair Cost Reduction: Timely maintenance can prevent up to 75% of costly repairs.
- Longevity: Well-maintained systems last 10-15 years, far exceeding the lifespan of poorly cared-for units.
- Warranty Compliance: Annual maintenance is often required by manufacturers to keep warranties valid, with 80% of claims denied without it.
- Air Quality Improvement: Maintaining HVAC systems enhances indoor air quality, lifting productivity in commercial spaces by 10% by minimizing allergens and pollutants.
Signs Your HVAC Needs Attention
Noticing indicators of problems early is crucial for prompt HVAC repair in Palmdale. Key indicators include:
- Strange sounds like grinding or squealing can signal issues.
- Rising energy bills, without more usage, show inefficiency.
- Fluctuating indoor temperatures suggest leaks or issues with ductwork.
- Frequent on-off cycling may be due to a faulty thermostat or compressor.
- Peculiar odors, be they musty or acrid, could signal electrical faults or mold.
Palmdale Residential HVAC Repair Services
In Palmdale, where temperatures soar, a working HVAC is essential. Homeowners frequently encounter problems such as refrigerant leaks and malfunctioning thermostats. Recognizing these problems and understanding the repair process reduces stress when breakdowns happen.
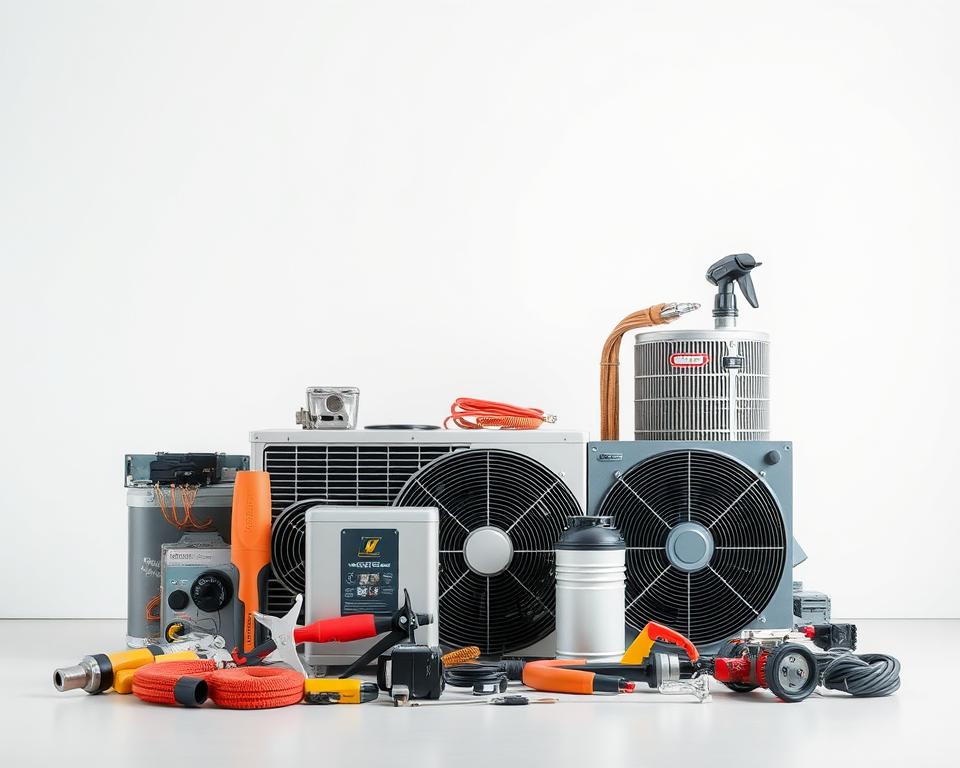
Common HVAC and AC Issues We Address
Common issues include:
- Thermostat malfunctions, leading to inconsistent indoor temperatures.
- Refrigerant leaks, that reduce cooling performance.
- Clogged filters, resulting in poor airflow and higher costs.
- Weak airflow, causing insufficient indoor comfort.
- Unusual noises coming from the unit, indicating potential mechanical failure.
Effective AC repair in Palmdale resolves these problems. Such repairs boost efficiency and lengthen the system’s life.
How to Troubleshoot Minor Problems
Prior to professional intervention in Palmdale, try these basic troubleshooting tips:
- Verify that your thermostat settings are correct.
- Examine your filters and change them if they appear dirty or obstructed.
- Look for any visible signs of refrigerant leaks around the unit.
- Confirm that vents are free from obstructions such as furniture.
Identifying these issues early may eliminate the need for emergency repairs, saving you money.
Seasonal Maintenance for HVAC Systems
Seasonal HVAC services are crucial for the system’s efficiency and longevity. Prepping for winter ensures smooth heating operation and minimal failure risks. These proactive steps reduce the likelihood of emergency services in Palmdale during winter. Regular maintenance prevents costly fixes, offering comfort during the cold months.
Getting Your HVAC Ready for Cold Weather
With winter approaching, residents in Palmdale need to focus on specific maintenance tasks. Tasks such as duct cleaning, furnace inspection, and exhaust system checks are crucial. Such maintenance increases both safety and performance in anticipation of cold weather. Maintained furnaces show a remarkable reduction—up to 95%—in failure rates compared to those poorly maintained.
Springtime AC Maintenance
With spring’s arrival, scheduling AC tune-ups is key for optimal performance in warmth. Regular service, though frequently neglected, may boost HVAC efficiency by as much as 15%. Verifying refrigerant levels is crucial since low levels hamper efficiency. Filter replacement and coil cleaning are key for enhanced performance and air quality. Proper upkeep yields both enhanced comfort and energy savings reaching up to 30%.
Expert Installation Services
High-quality installation by professionals is essential. Climate Control Heating and Cooling Inc., with over 36 years in the field, offers expert services in Palmdale. These enhance your system’s performance and efficiency. Proper setup can reduce utility expenses by 10-30% and prolong the life of AC units by up to a decade. Grasping the ins and outs of installation is vital for both homeowners and businesses.
Why Professional Installation Matters
Poor installation results in inefficiency, higher energy bills, and system breakdowns. Optimal operation is guaranteed through professional installation in Palmdale, which caters to your unique needs. Choosing experienced professionals minimizes errors, enhancing reliability and overall performance. Be it central air conditioning for large spaces, ductless mini-splits for efficiency, or window units for smaller areas, professional guidance is essential.
Our Step-by-Step Installation Method
Our HVAC installation process involves crucial steps to ensure superior service. We initiate with a detailed evaluation of your environment and requirements. We help you choose the best system and proceed with a precise installation. Typically, the steps are as follows:
Phase | Description |
---|---|
1. Preliminary Meeting | Assess your HVAC needs and preferences |
2. Unit Determination | Select the optimal system suited to your area |
3. Installation Scheduling | Schedule the installation at a time that works for you |
4. System Installation | Execute a careful and secure system installation |
5. Completion Verification | Test for optimal system operation |
6. Maintenance Guidance | Give guidance on proper maintenance practices |
Our detailed process ensures your HVAC system’s efficient operation for many years. Our 24/7 emergency HVAC services in Palmdale deliver fast, reliable repairs to restore your comfort immediately.
Prompt and Dependable Repairs
Fast and dependable repair services are key to preserving home comfort with your HVAC system. Unexpected issues necessitate knowing when repairs are needed. Our experienced HVAC repair experts in Palmdale quickly diagnose and resolve issues. Timely repairs avert minor issues from becoming major concerns.
Common HVAC and AC Issues
Many issues can affect HVAC and AC units, including:
- Faulty thermostats causing uneven temperature control.
- Refrigerant leakage that lowers the efficiency of cooling.
- Clogged filters that hinder airflow and increase energy costs.
- Weak airflow, resulting in reduced comfort levels.
- Unusual noises coming from the unit, indicating potential mechanical failure.
Effective repair of AC systems in Palmdale resolves these problems. Such repairs boost performance and increase longevity.
DIY HVAC Troubleshooting Tips
Before seeking professional HVAC repair in Palmdale, homeowners can try basic troubleshooting:
- Verify that the thermostat is correctly set.
- Inspect air filters and replace them if they are dirty or clogged.
- Search for obvious refrigerant leakage near the system.
- Confirm that vents remain unobstructed by any items.
This early detection can prevent the need for urgent repairs, thereby saving on maintenance expenses.
Seasonal HVAC Services
Yearly HVAC services are essential for optimal performance and extended lifespan. Preparing your system for winter guarantees reliable heating and lowers failure risks. Such measures help prevent urgent HVAC calls during cold spells in Palmdale. Routine upkeep avoids expensive repairs and maintains comfort throughout winter.
Preparing Your System for Winter
With winter approaching, residents in Palmdale must focus on essential HVAC maintenance. Tasks such as duct cleaning, furnace inspection, and exhaust system checks are critical. Such maintenance improves safety and efficiency, preparing your system for winter’s challenges.
Preparing Your AC for Spring
With spring’s arrival, scheduling AC tune-ups is key for optimal performance in warmth. Regular maintenance, although sometimes neglected, may improve HVAC performance by up to 15%. Ensure that refrigerant levels are adequate to avoid decreased efficiency. Filter replacement and coil cleaning are essential for enhanced operation and superior air quality. Proper maintenance results in both increased comfort and up to 30% energy savings.
Expert Installation Services
Expert installation of HVAC and air conditioning systems is vital.
In Palmdale, Climate Control Heating, Cooling & Plumbing has been a leader since 1987, offering premium installation services. Their installations boost both performance and efficiency. Proper setup can reduce utility expenses by 10-30% and prolong the life of AC units by up to a decade. Knowing the details of proper installation is essential for all, whether home or business.
The Importance of Expert Installation
Improper installation leads to reduced efficiency, increased costs, and potential failures. Professional installation in Palmdale ensures optimal system performance tailored to your specific requirements. Choosing skilled technicians prevents typical errors, ensuring superior performance and dependability. Be it central AC, ductless mini-splits, or window units, professional guidance is crucial.
How We Install Your System
We follow a detailed process to install your HVAC and air conditioning systems flawlessly. We begin with a comprehensive evaluation of your needs and space. We offer advice on choosing the perfect system, then install it with precision. The process generally unfolds as follows:
Step | Overview |
---|---|
1. First Meeting | Evaluate your system requirements and personal preferences |
2. Choosing the System | Choose the best unit for your environment |
3. Appointment Setting | Schedule the installation at your convenience |
4. Unit Setup | Carefully and safely install the HVAC system |
5. System Testing | Test for optimal system operation |
6. Post-Installation Support | Offer advice on upkeep and care |
Our detailed process ensures your HVAC system’s efficient operation for many years. Our Emergency HVAC services in Palmdale provide quick, effective solutions when you need them most, guaranteeing your comfort and peace of mind.
Prompt and Dependable Repairs
Speedy and trustworthy repairs are essential for keeping your HVAC and AC systems running smoothly. Sudden problems require immediate attention. Proficient technicians in Palmdale are skilled at rapidly addressing and fixing problems. This prevents minor issues from worsening into major complications.
Frequent Problems in HVAC and AC Units
Common issues include:
- Thermostat issues resulting in uneven temperatures.
- Leaks in refrigerant that reduce cooling effectiveness.
- Clogged filters that hinder airflow and increase energy costs.
- Poor air circulation leading to discomfort.
- Unusual noises coming from the unit, indicating potential mechanical failure.
Proper AC repair in Palmdale addresses these issues. This improves overall efficiency and extends system lifespan.
DIY Troubleshooting for Minor Issues
Before contacting an expert in Palmdale, try these basic troubleshooting measures:
- Check the thermostat settings to ensure they are properly adjusted.
- Review and replace air filters if they are clogged.
- Inspect the area around the unit for refrigerant leaks.
- Ensure that vents are not obstructed by furniture or other objects.
Early identification of these issues can avert emergency repairs and lower costs.
Seasonal HVAC Services
Seasonal HVAC services are crucial for the system’s efficiency and longevity. Getting your system ready for cold weather ensures efficient heating with lower failure chances. These preparations minimize emergency service calls during cold spells in Palmdale. Regular maintenance prevents costly fixes, offering comfort during the cold months.
Preparing Your System for Winter
As temperatures drop, it’s crucial for homeowners in Palmdale to perform key HVAC tasks. Ensure you clean ducts, examine the furnace, and inspect exhaust setups. Such maintenance improves safety and performance, preparing your system for winter’s challenges.
Spring AC Tune-Ups
As spring comes, arranging an AC tune-up is essential for peak performance in the heat. Consistent maintenance can improve efficiency by as much as 15%. Ensure refrigerant levels are adequate because low levels reduce performance. Changing filters and cleaning coils are crucial steps to better performance and air quality. Such upkeep not only enhances comfort but can also lower energy bills by up to 30%.
Quality HVAC and Air Conditioning Installation Services
Professional HVAC and air conditioning installation is crucial. Since 1987, Climate Control Heating, Cooling & Plumbing in Palmdale has been at the forefront of expert installation solutions. These services enhance your system’s performance and efficiency. Proper setup can reduce utility expenses by 10-30% and prolong the life of AC units by up to a decade. Knowing the details of proper installation is essential for all, whether residential or commercial.
The Importance of Expert Installation
Poor installation results in inefficiency, higher energy bills, and system breakdowns. Expert installation in Palmdale guarantees efficient operation customized to your individual needs. Hiring seasoned technicians avoids common mistakes, boosting reliability and performance. Whether it’s central air conditioning for expansive areas, ductless mini-splits for improved efficiency, or window units for compact spaces, expert advice is key.
Our Installation Process
We follow a detailed process to install your HVAC and air conditioning systems flawlessly. We begin with a comprehensive evaluation of your needs and space. We offer advice on choosing the perfect system, then install it with precision. Typically, the steps are:
Stage | Overview |
---|---|
1. Initial Consultation | Assess your HVAC needs and preferences |
2. Unit Determination | Select the optimal system suited to your area |
3. Appointment Setting | Set up a convenient time for installation |
4. System Installation | Perform a precise and secure installation |
5. System Testing | Test for optimal system operation |
6. Maintenance Guidance | Provide maintenance recommendations |
This thorough procedure guarantees long-term system efficiency. Our 24/7 emergency HVAC services in Palmdale offer rapid, effective repairs to ensure your comfort.
Prompt and Dependable Repairs
Speedy and trustworthy repairs are essential for keeping your HVAC and AC systems running smoothly. Unforeseen malfunctions call for prompt repairs. Our experienced repair experts in Palmdale quickly diagnose and resolve issues. This prevents minor issues from worsening into major complications.
Typical Issues in HVAC and air conditioning Systems
Frequent challenges encountered include:
- Thermostat malfunctions, leading to inconsistent indoor temperatures.
- Refrigerant leaks, which can compromise cooling efficiency.
- Dirty or blocked filters limiting airflow and driving up energy bills.
- Poor air circulation leading to discomfort.
- Strange sounds emanating from the system that suggest mechanical issues.
Timely repair services in Palmdale for AC resolve these issues. This improves overall efficiency and extends the system’s lifespan.
How to Troubleshoot Minor Problems
Before seeking professional HVAC repair in Palmdale, homeowners can try basic troubleshooting:
- Check the thermostat settings to ensure they are properly adjusted.
- Review and replace air filters if they are clogged.
- Look for any visible signs of refrigerant leaks around the unit.
- Ensure that vents are not obstructed by furniture or other objects.
This early detection can prevent the need for urgent repairs, thereby saving on maintenance expenses.
Year-Round HVAC Maintenance
Seasonal HVAC services are crucial for the system’s efficiency and longevity. Getting your system ready for cold weather ensures efficient heating with lower failure chances. These preparations minimize emergency service calls during cold spells in Palmdale. Consistent servicing saves on repair costs and provides warmth during cold weather.
Preparing Your System for Winter
As temperatures drop, it’s crucial for homeowners in Palmdale to perform key HVAC tasks. It’s important to clean ducts, inspect the furnace, and check exhaust systems. This care boosts safety and efficiency, readying your system for the cold’s demands.
Springtime air conditioning Maintenance
Spring is the ideal time to schedule air conditioning tune-ups for maximum efficiency. Regular servicing, although sometimes neglected, may boost HVAC performance by up to 15%. It’s vital to check refrigerant levels, as low levels diminish efficiency. Filter replacement and coil cleaning are essential for improved performance and air quality. Effective maintenance brings not just comfort but also energy savings of up to 30%.
Expert Installation Services
Expert installation of HVAC and AC systems is vital. In Palmdale, Climate Control Heating, Cooling & Plumbing has been a leader since 1987, providing premium installation services. These services enhance your system’s performance and efficiency. A proper setup can cut energy costs by 10-30% and increase the longevity of air conditioning units by up to 10 years. Knowing the details of proper installation is essential for all, whether residential or commercial.
Why Professional Installation Matters
Improper installation can lead to reduced efficiency, increased costs, and frequent failures. Professional installation in Palmdale ensures optimal performance tailored to your specific requirements. Hiring seasoned technicians avoids common mistakes, boosting reliability and performance. Be it central air conditioning, ductless systems, or window units, professional guidance is crucial.
How We Install Your System
Our HVAC and air conditioning installation process involves crucial steps to ensure superior service. The process initiates with a thorough assessment of your environment. Our experts help select the ideal system before installing it meticulously. The process generally unfolds as follows:
Step | Overview |
---|---|
1. Initial Consultation | Evaluate your system requirements and personal preferences |
2. System Selection | Pick the ideal HVAC system for your space |
3. Scheduling the Installation | Schedule the installation at your convenience |
4. System Installation | Carefully and safely install the HVAC system |
5. System Testing | Test for optimal system operation |
6. Post-Installation Support | Offer advice on upkeep and care |
Our meticulous process secures years of efficient operation for your system. Our 24/7 emergency HVAC services in Palmdale offer rapid, effective repairs to ensure your comfort.
Fast and Trustworthy Repairs
Rapid and reliable repair services are key to maintaining home comfort with your HVAC and AC units. Unforeseen malfunctions call for prompt repairs. Skilled technicians in HVAC repair in Palmdale adeptly identify and fix these problems swiftly. This prevents minor issues from worsening into major complications.
Typical Issues in HVAC and air conditioning Systems
Various problems can impair HVAC and AC units, such as:
- Thermostat issues resulting in uneven temperatures.
- Leaks in refrigerant that reduce cooling effectiveness.
- Dirty or blocked filters limiting airflow and driving up energy bills.
- Insufficient airflow causing a decline in comfort.
- Unusual noises coming from the unit, indicating potential mechanical failure.
Proper AC repair in Palmdale addresses these issues. This improves overall efficiency and extends the system’s lifespan.
DIY Troubleshooting for Minor Issues
Before contacting an expert in Palmdale, try these basic troubleshooting measures:
- Verify that the thermostat is correctly configured.
- Inspect air filters and replace them if they are dirty or clogged.
- Search for obvious signs of refrigerant leakage near the system.
- Ensure that vents are not obstructed by furniture or other objects.
Early identification of these issues can avert emergency repairs and lower costs.
Seasonal Maintenance Programs for HVAC
Yearly HVAC services are vital for ensuring efficiency and durability. Getting your system ready for cold weather ensures efficient heating with lower failure chances. These preparations minimize emergency service calls during cold spells in Palmdale. Consistent servicing saves on repair costs and provides warmth during cold weather.
Winterizing Your HVAC
With winter approaching, residents in Palmdale must focus on essential HVAC maintenance. Tasks such as duct cleaning, furnace inspection, and checking exhaust systems are vital. Such maintenance improves safety and performance, preparing your system for winter’s challenges.
Preparing Your AC for Spring
As spring comes, arranging an air conditioning tune-up is essential for peak performance in the heat. Regular servicing, although sometimes neglected, may boost HVAC performance by up to 15%. Ensure refrigerant levels are adequate because low levels reduce performance. Filter replacement and coil cleaning are essential for improved performance and air quality. Proper maintenance results in both increased comfort and energy savings reaching up to 30%.
Professional Installation Solutions
Professional HVAC and air conditioning installation is crucial. In Palmdale, Climate Control Heating, Cooling & Plumbing has led the industry since 1987, delivering expert services. These services enhance your system’s performance and efficiency. A proper setup can cut energy costs by 10-30% and increase the longevity of air conditioning units by up to 10 years. Grasping the ins and outs of installation is vital for both homeowners and businesses.
Why Professional Installation Matters
Substandard installation may cause inefficiency, elevated bills, and system malfunctions. Optimal operation is guaranteed through professional installation in Palmdale, which caters to your unique needs. Choosing skilled technicians prevents typical errors, ensuring superior performance and dependability. Whether it’s central air conditioning for expansive areas, ductless mini-splits for improved efficiency, or window units for compact spaces, expert advice is key.
Our Step-by-Step Installation Method
Our HVAC and air conditioning installation process involves crucial steps to ensure superior service. We begin with a comprehensive evaluation of your needs and space. Our experts help select the ideal system before installing it meticulously. The process generally unfolds as follows:
Phase | Details |
---|---|
1. Preliminary Assessment | Determine your specific HVAC and AC needs |
2. Choosing the System | Choose the best unit for your environment |
3. Scheduling the Installation | Set up a convenient time for installation |
4. System Installation | Carefully and safely install the HVAC system |
5. System Testing | Verify that the system operates flawlessly |
6. Maintenance Guidance | Provide maintenance recommendations |
Our meticulous process secures years of efficient operation for your system. Our 24/7 emergency HVAC services in Palmdale offer rapid, effective repairs to ensure your comfort.
Fast and Trustworthy Repairs
Quick and dependable fixes are crucial for HVAC and air conditioning systems to ensure home comfort. Unforeseen malfunctions call for prompt repairs. Our experienced repair experts in Palmdale quickly diagnose and resolve issues. This prevents minor issues from worsening into major complications.
Frequent Problems in HVAC and air conditioning Units
Various problems can impair HVAC and AC units, such as:
- Thermostat malfunctions, leading to inconsistent indoor temperatures.
- Leaks in refrigerant that reduce cooling effectiveness.
- Dirty or blocked filters limiting airflow and driving up energy bills.
- Poor air circulation leading to discomfort.
- Strange sounds emanating from the system that suggest mechanical issues.
Proper air conditioning repair in Palmdale addresses these issues. It enhances system performance and prolongs its durability.
Basic Troubleshooting Steps
Prior to calling for professional repair in Palmdale, you can attempt simple troubleshooting steps:
- Check the thermostat settings to ensure they are properly adjusted.
- Examine your filters and change them if they appear obstructed.
- Inspect the area around the unit for refrigerant leaks.
- Make sure that nothing is blocking the vents.
Detecting problems early helps avoid costly repairs, saving money.
Seasonal Maintenance Programs for HVAC
Seasonal HVAC services are crucial for the system’s efficiency and longevity. Prepping for winter ensures smooth heating operation and minimal failure risks. Such measures help prevent urgent repairs during winter in Palmdale. Regular maintenance prevents costly fixes, offering comfort during the cold months.
Winterizing Your HVAC
As the cold season nears, homeowners in Palmdale should prioritize certain HVAC upkeep tasks. It’s important to clean ducts, inspect the furnace, and check exhaust systems. This care boosts safety and efficiency, readying your system for the cold’s demands.
Preparing Your Air Conditioning for Spring
Spring is the ideal time to schedule air conditioning tune-ups for maximum efficiency. Regular servicing, although sometimes neglected, may boost HVAC performance by up to 15%. Ensure refrigerant levels are adequate because low levels reduce performance. Replacing filters and cleaning coils are key actions for optimal operation and enhanced air quality. Such upkeep not only enhances comfort but can also lower energy bills by up to 30%.
Expert Installation Services
Professional HVAC and AC installation is crucial. In Palmdale, Climate Control Heating, Cooling & Plumbing has been a leader since 1987, providing premium installation services. These services enhance your system’s performance and efficiency. Correct installation may lower utility bills by 10-30% and extend the lifespan of AC systems by up to 10 years. Grasping the ins and outs of installation is vital for both homeowners and businesses.
Benefits of Professional Installation
Poor installation results in inefficiency, higher energy bills, and system breakdowns. Optimal operation is guaranteed through professional installation in Palmdale, which caters to your unique needs. Engaging experienced professionals minimizes errors and enhances system reliability. Whether it’s central air conditioning for expansive areas, ductless mini-splits for improved efficiency, or window units for compact spaces, expert advice is key.
How We Install Your System
Our installation procedure consists of key stages that guarantee excellent results. We begin with a comprehensive evaluation of your needs and space. We guide you in choosing the best system and then execute the installation precisely. Typically, the steps are:
Stage | Details |
---|---|
1. Preliminary Assessment | Evaluate your system requirements and personal preferences |
2. Unit Determination | Select the optimal system suited to your area |
3. Scheduling the Installation | Set up a convenient time for installation |
4. Unit Setup | Execute the installation with accuracy and safety |
5. System Testing | Conduct final tests to ensure peak performance |
6. Maintenance Guidance | Give guidance on proper system care |
Our detailed process ensures your HVAC system’s efficient operation for many years. Our Emergency HVAC services in Palmdale provide quick, effective solutions when you need them most, guaranteeing your comfort and peace of mind.
Fast and Trustworthy Repairs
Rapid and reliable repair services are key to maintaining home comfort with your HVAC and AC units. Unforeseen malfunctions call for prompt repairs. Proficient technicians in Palmdale are skilled at rapidly addressing and fixing problems. This prevents minor issues from worsening into major complications.
Typical Issues in HVAC and air conditioning Systems
Common issues include:
- Thermostat malfunctions, leading to inconsistent indoor temperatures.
- Refrigerant leaks, which can compromise cooling efficiency.
- Clogged filters that hinder airflow and increase energy costs.
- Weak airflow, resulting in reduced comfort levels.
- Odd noises that may signal impending mechanical breakdowns.
Effective repair of air conditioning systems in Palmdale fixes these problems. This improves overall efficiency and extends the system’s lifespan.
How to Troubleshoot Minor Problems
Before seeking professional HVAC repair in Palmdale, homeowners can try basic troubleshooting:
- Confirm the thermostat settings are appropriate.
- Review and replace air filters if they are clogged.
- Look for any visible signs of refrigerant leaks around the unit.
- Ensure that vents are not obstructed by furniture or other objects.
Detecting problems early helps avoid costly repairs, saving money.
Seasonal HVAC Services
Seasonal HVAC services are crucial for the system’s efficiency and longevity. Prepping for winter ensures smooth heating operation and minimal failure risks. These preparations minimize emergency service calls during cold spells in Palmdale. Consistent servicing saves on repair costs and provides warmth during cold weather.
Getting Your HVAC Ready for Cold Weather
As temperatures drop, it’s crucial for homeowners in Palmdale to perform key HVAC tasks. Tasks such as duct cleaning, furnace inspection, and checking exhaust systems are vital. This care boosts safety and efficiency, readying your system for the cold’s demands.
Springtime air conditioning Maintenance
As spring comes, arranging an air conditioning tune-up is essential for peak performance in the heat. Routine maintenance, often overlooked, can enhance HVAC efficiency by up to 15%. Ensure refrigerant levels are adequate because low levels reduce performance. Replacing filters and cleaning coils are key actions for optimal operation and enhanced air quality. Proper maintenance results in both increased comfort and energy savings reaching up to 30%.
Professional Installation Solutions
Expert installation of HVAC and AC systems is vital. Since 1987, Climate Control Heating, Cooling & Plumbing in Palmdale has been at the forefront of expert installation solutions. These services enhance your system’s performance and efficiency. A proper setup can cut energy costs by 10-30% and increase the longevity of air conditioning units by up to 10 years. Knowing the details of proper installation is essential for all, whether residential or commercial.
The Importance of Expert Installation
Poor installation results in inefficiency, higher energy bills, and system breakdowns. Expert installation in Palmdale guarantees efficient operation customized to your individual needs. Choosing skilled technicians prevents typical errors, ensuring superior performance and dependability. Whether you need central air conditioning, ductless mini-splits, or window units, expert consultation is essential.
Our Installation Process
We follow a detailed process to install your HVAC and AC systems flawlessly. We begin with a comprehensive evaluation of your needs and space. Our experts help select the ideal system before installing it meticulously. Our process is structured as follows:
Phase | Details |
---|---|
1. Preliminary Assessment | Evaluate your system requirements and personal preferences |
2. Unit Determination | Pick the ideal HVAC system for your space |
3. Scheduling the Installation | Set up a convenient time for installation |
4. System Installation | Execute the installation with accuracy and safety |
5. Completion Verification | Verify that the system operates flawlessly |
6. Post-Installation Support | Offer advice on upkeep and care |
This thorough procedure guarantees long-term system efficiency. Our 24/7 emergency HVAC services in Palmdale offer rapid, effective repairs to ensure your comfort.
Fast and Trustworthy Repairs
Speedy and trustworthy repairs are essential for keeping your HVAC and AC systems running smoothly. Unforeseen malfunctions call for prompt repairs. Proficient technicians in Palmdale are skilled at rapidly addressing and fixing problems. This prevents minor issues from worsening into major complications.
Common HVAC and AC Issues
Frequent challenges encountered include:
- Thermostat malfunctions, leading to inconsistent indoor temperatures.
- Refrigerant leaks, which can compromise cooling efficiency.
- Clogged filters that hinder airflow and increase energy costs.
- Insufficient airflow causing a decline in comfort.
- Odd noises that may signal impending mechanical breakdowns.
Timely repair services in Palmdale for AC resolve these issues. This improves overall efficiency and extends the system’s lifespan.
How to Troubleshoot Minor Problems
Before seeking professional HVAC repair in Palmdale, homeowners can try basic troubleshooting:
- Verify that the thermostat is correctly configured.
- Inspect air filters and replace them if they are dirty or clogged.
- Inspect the area around the unit for refrigerant leaks.
- Confirm that vents remain clear of obstructions.
Detecting problems early helps avoid costly repairs, saving money.
How to Pick the Best AC System
Choosing the ideal air conditioning system in Palmdale requires careful consideration. Identifying your unique requirements is crucial, as it affects both system performance and comfort. Every unit is engineered for particular functions. Energy efficiency ratings are important to ensure long-term economic benefits.
Factors to Consider When Buying an AC
When replacing your air conditioning unit in Palmdale, several factors must be considered.
- Home Size: The size of your home determines the cooling requirements. Ensuring the proper BTU calculation is key for optimal performance.
- Energy Efficiency: Aim for air conditioning units with superior SEER ratings. They consume power more efficiently, cutting down on energy expenses.
- Climate: The severe summer heat in North Carolina underscores the need for effective cooling. For moderate conditions, heat pumps are highly effective.
- Budget: Consider both the initial expense and long-term energy savings. Economical options might incur extra costs in maintenance and energy use.
Eco-Friendly Air Conditioning Models
Opting for energy-efficient AC systems offers environmental and comfort advancements. Consider ductless mini-splits for flexibility and efficiency, particularly if your house lacks ductwork. For HVAC installation in Palmdale, geothermal systems can be a smart choice. They substantially reduce energy consumption.
Professional Installation Solutions
Expert installation is vital. With 36+ years of expertise, Climate Control Heating, Cooling & Plumbing Inc. provides expert installation in Palmdale. Their installations improve system efficiency and performance. Proper installation may cut energy costs by 10-30% and increase the longevity of air conditioning units by up to 10 years. Understanding installation intricacies is key for both residential and commercial clients.
The Importance of Expert Installation
Substandard installation may cause inefficiency, elevated bills, and system malfunctions. Expert installation in Palmdale guarantees efficient operation customized to your individual needs. Engaging experienced professionals minimizes errors and enhances system reliability. Whether it’s central AC for expansive areas, ductless mini-splits for improved efficiency, or window units for compact spaces, expert advice is key.
Our Installation Process
Our installation procedure consists of key stages that guarantee excellent results. We begin with a comprehensive evaluation of your needs and space. Our experts help select the ideal system before installing it meticulously. The process generally unfolds as follows:
Phase | Overview |
---|---|
1. First Meeting | Evaluate your system requirements and personal preferences |
2. Unit Determination | Choose the best unit for your environment |
3. Scheduling the Installation | Schedule the installation at your convenience |
4. Unit Setup | Execute the installation with accuracy and safety |
5. Final Checks | Conduct final tests to ensure peak performance |
6. Post-Installation Support | Give guidance on proper system care |
Our meticulous process secures years of efficient operation for your system. In Palmdale, our emergency services deliver prompt, reliable solutions to restore comfort and security.
Quick and Reliable Repairs
Quick and dependable fixes are crucial for HVAC and air conditioning systems to ensure home comfort. Unforeseen malfunctions call for prompt repairs. Skilled technicians in HVAC repair in Palmdale adeptly identify and fix these problems swiftly. Such prompt action stops small problems from escalating.
Common HVAC and AC Issues
Common issues include:
- Thermostat malfunctions, leading to inconsistent indoor temperatures.
- Refrigerant leaks, which can compromise cooling efficiency.
- Obstructed filters that decrease efficiency and raise costs.
- Insufficient airflow causing a decline in comfort.
- Strange sounds emanating from the system that suggest mechanical issues.
Proper air conditioning repair in Palmdale addresses these issues. Such repairs boost performance and increase longevity.
Basic Troubleshooting Steps
Before seeking professional HVAC repair in Palmdale, homeowners can try basic troubleshooting:
- Verify that the thermostat is correctly configured.
- Examine your filters and change them if they appear obstructed.
- Search for obvious signs of refrigerant leakage near the system.
- Ensure that vents are not obstructed by furniture or other objects.
Detecting problems early helps avoid costly repairs, saving money.
How to Pick the Best AC System
Choosing the ideal AC system in Palmdale requires careful consideration. It’s vital to identify your unique needs, as this influences the system’s efficacy and your comfort. Every unit is engineered for particular functions. Being aware of energy efficiency ratings is also key to economizing in the future.
Important Aspects When Choosing an AC
Several critical aspects must be evaluated when upgrading your air conditioning in Palmdale.
- Home Size: Your space’s size dictates the necessary cooling capacity. Ensuring the proper BTU calculation is key for optimal performance.
- Energy Efficiency: Select AC systems with excellent SEER ratings. They operate more efficiently, thereby lowering energy costs.
- Climate: The intense summers in North Carolina highlight the significance of efficient cooling. Heat pumps work best in moderate climates.
- Budget: Balance upfront costs with expected energy savings. Economical options might incur extra costs in maintenance and energy use.
Eco-Friendly Air Conditioning Models
Opting for energy-efficient AC systems offers environmental and comfort advancements. For houses without ductwork, ductless mini-splits provide excellent efficiency and adaptability. When contemplating HVAC installation in Palmdale, think about geothermal systems. They substantially reduce energy consumption.
Professional Installation Solutions
Quality installation by professionals is essential. Climate Control Heating, Cooling & Plumbing Inc., with over 36 years in the field, offers expert services in Palmdale. Their installations improve system efficiency and performance. A correct installation can lower utility bills by 10-30% and extend the lifespan of air conditioning systems by up to 10 years. Knowing the details of proper installation is essential for all, whether residential or commercial.
Why Professional Installation Matters
Poor installation results in inefficiency, higher energy bills, and system breakdowns. Professional installation in Palmdale ensures optimal performance tailored to your specific requirements. Engaging experienced professionals minimizes errors and enhances system reliability. Be it central air conditioning, ductless systems, or window units, professional guidance is crucial.
How We Install Your System
Our HVAC and AC installation process involves crucial steps to ensure superior service. It starts with an in-depth analysis of your area and requirements. We guide you in choosing the best system and then execute the installation precisely. Our process is structured as follows:
Step | Description |
---|---|
1. Preliminary Assessment | Evaluate your system requirements and personal preferences |
2. Unit Determination | Choose the best unit for your environment |
3. Appointment Setting | Set up a convenient time for installation |
4. Installation Process | Carefully and safely install the HVAC system |
5. Completion Verification | Verify that the system operates flawlessly |
6. Post-Installation Support | Offer advice on upkeep and care |
This thorough procedure guarantees long-term system efficiency. In Palmdale, our emergency services deliver prompt, reliable solutions to restore comfort and security.
Fast and Trustworthy Repairs
Speedy and trustworthy repairs are essential for keeping your HVAC and AC systems running smoothly. Sudden problems require immediate attention. Skilled technicians in HVAC repair in Palmdale adeptly identify and fix these problems swiftly. Such prompt action stops small problems from escalating.
Common HVAC and AC Issues
Frequent challenges encountered include:
- Faulty thermostats causing irregular temperature control.
- Refrigerant leaks, which can compromise cooling efficiency.
- Clogged filters that hinder airflow and increase energy costs.
- Poor air circulation leading to discomfort.
- Unusual noises coming from the unit, indicating potential mechanical failure.
Proper air conditioning repair in Palmdale addresses these issues. Such repairs boost performance and increase longevity.
DIY Troubleshooting for Minor Issues
Prior to calling for professional repair in Palmdale, you can attempt simple troubleshooting steps:
- Confirm the thermostat settings are appropriate.
- Review and replace air filters if they are clogged.
- Look for any visible signs of refrigerant leaks around the unit.
- Confirm that vents remain clear of obstructions.
Detecting problems early helps avoid costly repairs, saving money.
Choosing the Right AC System
Choosing the ideal AC system in Palmdale requires careful consideration. Knowing your specific needs is key to ensuring the system’s effectiveness and your overall comfort. Each model is designed with specific functions in mind. Energy efficiency ratings are important to ensure long-term economic benefits.
Key Considerations for AC Purchases
Multiple factors are crucial when selecting a new AC system in Palmdale.
- Home Size: Home dimensions determine the required BTUs for efficient cooling. Calculating the correct BTUs is crucial for efficient cooling.
- Energy Efficiency: Select AC systems with excellent SEER ratings. They operate more efficiently, thereby lowering energy costs.
- Climate: The intense summers in North Carolina highlight the significance of efficient cooling. Heat pumps work best in moderate climates.
- Budget: Weigh the purchase price against potential energy cost reductions. Cheaper units may lead to higher future repair and energy costs.
Eco-Friendly Air Conditioning Models
Selecting energy-saving AC models enhances both comfort and sustainability. For houses without ductwork, ductless mini-splits provide excellent efficiency and adaptability. When contemplating HVAC installation in Palmdale, think about geothermal systems. They substantially reduce energy consumption.
Quality HVAC and air conditioning Installation Services
Quality installation by professionals is essential. With 36+ years of expertise, Climate Control Heating, Cooling & Plumbing Inc. provides expert installation in Palmdale. Their installations improve system efficiency and performance. Proper installation may cut energy costs by 10-30% and increase the longevity of AC units by up to 10 years. Knowing the details of proper installation is essential for all, whether residential or commercial.
Benefits of Professional Installation
Substandard installation may cause inefficiency, elevated bills, and system malfunctions. Expert installation in Palmdale guarantees efficient operation customized to your individual needs. Choosing skilled technicians prevents typical errors, ensuring superior performance and dependability. Whether it’s central AC for expansive areas, ductless mini-splits for improved efficiency, or window units for compact spaces, expert advice is key.
Our Installation Process
We follow a detailed process to install your HVAC and AC systems flawlessly. The process initiates with a thorough assessment of your environment. We offer advice on choosing the perfect system, then install it with precision. Our process is structured as follows:
Stage | Overview |
---|---|
1. Initial Consultation | Determine your specific HVAC and air conditioning needs |
2. System Selection | Choose the best unit for your environment |
3. Installation Scheduling | Arrange a suitable time for the setup |
4. Installation Process | Execute the installation with accuracy and safety |
5. Completion Verification | Conduct final tests to ensure peak performance |
6. Upkeep Advice | Give guidance on proper system care |
This thorough procedure guarantees long-term system efficiency. Our 24/7 emergency HVAC services in Palmdale offer rapid, effective repairs to ensure your comfort.
Fast and Trustworthy Repairs
Quick and dependable fixes are crucial for HVAC and AC systems to ensure home comfort. Unforeseen malfunctions call for prompt repairs. Our experienced repair experts in Palmdale quickly diagnose and resolve issues. This prevents minor issues from worsening into major complications.
Common HVAC and AC Issues
Common issues include:
- Thermostat issues resulting in uneven temperatures.
- Leaks in refrigerant that reduce cooling effectiveness.
- Obstructed filters that decrease efficiency and raise costs.
- Poor air circulation leading to discomfort.
- Strange sounds emanating from the system that suggest mechanical issues.
Timely repair services in Palmdale for AC resolve these issues. This improves overall efficiency and extends the system’s lifespan.
How to Troubleshoot Minor Problems
Before seeking professional HVAC repair in Palmdale, homeowners can try basic troubleshooting:
- Check the thermostat settings to ensure they are properly adjusted.
- Examine your filters and change them if they appear obstructed.
- Look for any visible signs of refrigerant leaks around the unit.
- Make sure that nothing is blocking the vents.
This early detection can prevent the need for urgent repairs, thereby saving on maintenance expenses.
Selecting the Ideal Air Conditioning System
Selecting the right air conditioning system for your home in Palmdale is a process that demands attention to detail. Knowing your specific needs is key to ensuring the system’s effectiveness and your overall comfort. Each model is designed with specific functions in mind. Understanding energy efficiency ratings is critical for future cost savings.
Key Considerations for AC Purchases
When replacing your AC unit in Palmdale, several factors must be considered.
- Home Size: Your space’s size dictates the necessary cooling capacity. Accurate BTU calculation is essential for efficient cooling.
- Energy Efficiency: Select AC systems with excellent SEER ratings. These models use electricity more effectively, reducing energy bills.
- Climate: The intense summers in North Carolina highlight the significance of efficient cooling. For moderate conditions, heat pumps are highly effective.
- Budget: Balance upfront costs with expected energy savings. Economical options might incur extra costs in maintenance and energy use.
High-Efficiency Systems
Opting for energy-efficient AC systems offers environmental and comfort advancements. Consider ductless mini-splits for flexibility and efficiency, particularly if your house lacks ductwork. When contemplating HVAC installation in Palmdale, think about geothermal systems. They significantly lower energy consumption.
Professional Installation Solutions
Professional installation is crucial. Climate Control Heating, Cooling & Plumbing Inc., with over 36 years in the field, offers expert services in Palmdale. Their installations improve system efficiency and performance. Proper installation may cut energy costs by 10-30% and increase the longevity of air conditioning units by up to 10 years. Grasping the ins and outs of installation is vital for both homeowners and businesses.
Benefits of Professional Installation
Poor installation results in inefficiency, higher energy bills, and system breakdowns. Optimal operation is guaranteed through professional installation in Palmdale, which caters to your unique needs. Choosing skilled technicians prevents typical errors, ensuring superior performance and dependability. Be it central air conditioning, ductless systems, or window units, professional guidance is crucial.
Our Installation Process
We follow a detailed process to install your HVAC and air conditioning systems flawlessly. It starts with an in-depth analysis of your area and requirements. We guide you in choosing the best system and then execute the installation precisely. Our process is structured as follows:
Stage | Description |
---|---|
1. First Meeting | Assess your HVAC needs and preferences |
2. Choosing the System | Choose the best unit for your environment |
3. Installation Scheduling | Arrange a suitable time for the setup |
4. Unit Setup | Carefully and safely install the HVAC system |
5. System Testing | Conduct final tests to ensure peak performance |
6. Post-Installation Support | Provide maintenance recommendations |
Our meticulous process secures years of efficient operation for your system. Our 24/7 emergency HVAC services in Palmdale offer rapid, effective repairs to ensure your comfort.
Prompt and Dependable Repairs
Rapid and reliable repair services are key to maintaining home comfort with your HVAC and AC units. Unforeseen malfunctions call for prompt repairs. Our experienced repair experts in Palmdale quickly diagnose and resolve issues. Early repairs help avoid larger, costlier issues.
Frequent Problems in HVAC and AC Units
Frequent challenges encountered include:
- Thermostat issues resulting in uneven temperatures.
- Leaks in refrigerant that reduce cooling effectiveness.
- Dirty or blocked filters limiting airflow and driving up energy bills.
- Weak airflow, resulting in reduced comfort levels.
- Strange sounds emanating from the system that suggest mechanical issues.
Proper air conditioning repair in Palmdale addresses these issues. This improves overall efficiency and extends the system’s lifespan.
How to Troubleshoot Minor Problems
Prior to calling for professional repair in Palmdale, you can attempt simple troubleshooting steps:
- Verify that the thermostat is correctly configured.
- Review and replace air filters if they are clogged.
- Search for obvious signs of refrigerant leakage near the system.
- Confirm that vents remain clear of obstructions.
Early identification of these issues can avert emergency repairs and lower costs.
Professional Installation Solutions
High-quality installation by professionals is essential. With 36+ years of expertise, Climate Control Heating, Cooling & Plumbing Inc. provides expert installation in Palmdale. Expert installation boosts both performance and energy efficiency. Proper setup can reduce utility expenses by 10-30% and prolong the life of AC units by up to a decade. Grasping the ins and outs of installation is vital for both homeowners and businesses.
Why Professional Installation Matters
Poor installation results in inefficiency, higher energy bills, and system breakdowns. Expert installation in Palmdale guarantees efficient operation customized to your individual needs. Choosing skilled technicians prevents typical errors, ensuring superior performance and dependability. Whether you need central AC, ductless mini-splits, or window units, expert consultation is essential.
How We Install Your System
Our HVAC and AC installation process involves crucial steps to ensure superior service. The process initiates with a thorough assessment of your environment. Our experts help select the ideal system before installing it meticulously. Typically, the steps are:
Stage | Details |
---|---|
1. First Meeting | Determine your specific HVAC and air conditioning needs |
2. Choosing the System | Choose the best unit for your environment |
3. Appointment Setting | Arrange a suitable time for the setup |
4. Unit Setup | Carefully and safely install the HVAC system |
5. Final Checks | Conduct final tests to ensure peak performance |
6. Maintenance Guidance | Offer advice on upkeep and care |
This thorough procedure guarantees long-term system efficiency. In Palmdale, our emergency services deliver prompt, reliable solutions to restore comfort and security.
Prompt and Dependable Repairs
Quick and dependable fixes are crucial for HVAC and AC systems to ensure home comfort. Unexpected issues necessitate knowing when repairs are needed. Proficient technicians in Palmdale are skilled at rapidly addressing and fixing problems. Early repairs help avoid larger, costlier issues.
Frequent Problems in HVAC and air conditioning Units
Common issues include:
- Thermostat malfunctions, leading to inconsistent indoor temperatures.
- Refrigerant loss that diminishes air conditioning performance.
- Dirty or blocked filters limiting airflow and driving up energy bills.
- Weak airflow, resulting in reduced comfort levels.
- Strange sounds emanating from the system that suggest mechanical issues.
Proper air conditioning repair in Palmdale addresses these issues. Such repairs boost performance and increase longevity.
Basic Troubleshooting Steps
Before contacting an expert in Palmdale, try these basic troubleshooting measures:
- Confirm the thermostat settings are appropriate.
- Inspect air filters and replace them if they are dirty or clogged.
- Search for obvious signs of refrigerant leakage near the system.
- Ensure that vents are not obstructed by furniture or other objects.
Early identification of these issues can avert emergency repairs and lower costs.
Expert Installation Services
High-quality installation by professionals is essential. In Palmdale, Climate Control Heating, Cooling & Plumbing Inc. has over 36 years of experience delivering top-notch services. Expert installation boosts both performance and energy efficiency. Proper installation may cut energy costs by 10-30% and increase the longevity of AC units by up to 10 years. Grasping the ins and outs of installation is vital for both homeowners and businesses.
Benefits of Professional Installation
Substandard installation may cause inefficiency, elevated bills, and system malfunctions. Optimal operation is guaranteed through professional installation in Palmdale, which caters to your unique needs. Hiring seasoned technicians avoids common mistakes, boosting reliability and performance. Whether it’s central AC for expansive areas, ductless mini-splits for improved efficiency, or window units for compact spaces, expert advice is key.
Our Installation Process
Our HVAC and air conditioning installation process involves crucial steps to ensure superior service. We begin with a comprehensive evaluation of your needs and space. We offer advice on choosing the perfect system, then install it with precision. The process generally unfolds as follows:
Phase | Description |
---|---|
1. Preliminary Assessment | Assess your HVAC needs and preferences |
2. Choosing the System | Select the optimal system suited to your area |
3. Appointment Setting | Arrange a suitable time for the setup |
4. Unit Setup | Perform a precise and secure installation |
5. Completion Verification | Conduct final tests to ensure peak performance |
6. Post-Installation Support | Provide maintenance recommendations |
This thorough procedure guarantees long-term system efficiency. Our Emergency HVAC services in Palmdale provide quick, effective solutions when you need them most, guaranteeing your comfort and peace of mind.
Fast and Trustworthy Repairs
Quick and dependable fixes are crucial for HVAC and air conditioning systems to ensure home comfort. Unforeseen malfunctions call for prompt repairs. Skilled technicians in HVAC repair in Palmdale adeptly identify and fix these problems swiftly. This prevents minor issues from worsening into major complications.
Common HVAC and AC Issues
Common issues include:
- Thermostat issues resulting in uneven temperatures.
- Refrigerant loss that diminishes air conditioning performance.
- Obstructed filters that decrease efficiency and raise costs.
- Insufficient airflow causing a decline in comfort.
- Strange sounds emanating from the system that suggest mechanical issues.
Timely repair services in Palmdale for air conditioning resolve these issues. This improves overall efficiency and extends the system’s lifespan.
How to Troubleshoot Minor Problems
Before contacting an expert in Palmdale, try these basic troubleshooting measures:
- Confirm the thermostat settings are appropriate.
- Examine your filters and change them if they appear obstructed.
- Inspect the area around the unit for refrigerant leaks.
- Make sure that nothing is blocking the vents.
Detecting problems early helps avoid costly repairs, saving money.
Expert Installation Services
High-quality installation by professionals is essential. In Palmdale, Climate Control Heating, Cooling & Plumbing Inc. has over 36 years of experience delivering top-notch services. Their installations improve system efficiency and performance. A correct installation can lower utility bills by 10-30% and extend the lifespan of AC systems by up to 10 years. Grasping the ins and outs of installation is vital for both homeowners and businesses.
Why Professional Installation Matters
Substandard installation may cause inefficiency, elevated bills, and system malfunctions. Optimal operation is guaranteed through professional installation in Palmdale, which caters to your unique needs. Engaging experienced professionals minimizes errors and enhances system reliability. Be it central air conditioning, ductless systems, or window units, professional guidance is crucial.
How We Install Your System
Our HVAC and AC installation process involves crucial steps to ensure superior service. We begin with a comprehensive evaluation of your needs and space. We offer advice on choosing the perfect system, then install it with precision. The process generally unfolds as follows:
Step | Overview |
---|---|
1. Initial Consultation | Assess your HVAC needs and preferences |
2. Choosing the System | Choose the best unit for your environment |
3. Installation Scheduling | Schedule the installation at your convenience |
4. Unit Setup | Carefully and safely install the HVAC system |
5. Final Checks | Conduct final tests to ensure peak performance |
6. Maintenance Guidance | Offer advice on upkeep and care |
Our meticulous process secures years of efficient operation for your system. In Palmdale, our emergency services deliver prompt, reliable solutions to restore comfort and security.
Prompt and Dependable Repairs
Speedy and trustworthy repairs are essential for keeping your HVAC and air conditioning systems running smoothly. Unexpected issues necessitate knowing when repairs are needed. Proficient technicians in Palmdale are skilled at rapidly addressing and fixing problems. Such prompt action stops small problems from escalating.
Frequent Problems in HVAC and AC Units
Various problems can impair HVAC and air conditioning units, such as:
- Thermostat issues resulting in uneven temperatures.
- Refrigerant loss that diminishes AC performance.
- Clogged filters that hinder airflow and increase energy costs.
- Weak airflow, resulting in reduced comfort levels.
- Odd noises that may signal impending mechanical breakdowns.
Effective repair of air conditioning systems in Palmdale fixes these problems. This improves overall efficiency and extends the system’s lifespan.
Basic Troubleshooting Steps
Prior to calling for professional repair in Palmdale, you can attempt simple troubleshooting steps:
- Confirm the thermostat settings are appropriate.
- Review and replace air filters if they are clogged.
- Inspect the area around the unit for refrigerant leaks.
- Make sure that nothing is blocking the vents.
Early identification of these issues can avert emergency repairs and lower costs.
Professional Installation Solutions
High-quality installation by professionals is essential. With 36+ years of expertise, Climate Control Heating, Cooling & Plumbing Inc. provides expert installation in Palmdale. Expert installation boosts both performance and energy efficiency. Proper setup can reduce utility expenses by 10-30% and prolong the life of air conditioning units by up to a decade. Knowing the details of proper installation is essential for all, whether residential or commercial.
The Importance of Expert Installation
Poor installation results in inefficiency, higher energy bills, and system breakdowns. Expert installation in Palmdale guarantees efficient operation customized to your individual needs. Hiring seasoned technicians avoids common mistakes, boosting reliability and performance. Be it central AC, ductless systems, or window units, professional guidance is crucial.
Our Step-by-Step Installation Method
Our installation procedure consists of key stages that guarantee excellent results. We begin with a comprehensive evaluation of your needs and space. We guide you in choosing the best system and then execute the installation precisely. Typically, the steps are:
Phase | Description |
---|---|
1. First Meeting | Evaluate your system requirements and personal preferences |
2. System Selection | Choose the best unit for your environment |
3. Appointment Setting | Schedule the installation at your convenience |
4. System Installation | Carefully and safely install the HVAC system |
5. Final Checks | Verify that the system operates flawlessly |
6. Maintenance Guidance | Give guidance on proper system care |
Our meticulous process secures years of efficient operation for your system. In Palmdale, our emergency services deliver prompt, reliable solutions to restore comfort and security.
Prompt and Dependable Repairs
Rapid and reliable repair services are key to maintaining home comfort with your HVAC and AC units. Unforeseen malfunctions call for prompt repairs. Our experienced repair experts in Palmdale quickly diagnose and resolve issues. Early repairs help avoid larger, costlier issues.
Common HVAC and AC Issues
Various problems can impair HVAC and AC units, such as:
- Thermostat issues resulting in uneven temperatures.
- Refrigerant loss that diminishes AC performance.
- Obstructed filters that decrease efficiency and raise costs.
- Insufficient airflow causing a decline in comfort.
- Odd noises that may signal impending mechanical breakdowns.
Timely repair services in Palmdale for air conditioning resolve these issues. It enhances system performance and prolongs its durability.
DIY Troubleshooting for Minor Issues
Before seeking professional HVAC repair in Palmdale, homeowners can try basic troubleshooting:
- Check the thermostat settings to ensure they are properly adjusted.
- Examine your filters and change them if they appear obstructed.
- Look for any visible signs of refrigerant leaks around the unit.
- Confirm that vents remain clear of obstructions.
Early identification of these issues can avert emergency repairs and lower costs.
Quality HVAC and AC Installation Services
High-quality installation by professionals is essential. In Palmdale, Climate Control Heating, Cooling & Plumbing Inc. has over 36 years of experience delivering top-notch services. Expert installation boosts both performance and energy efficiency. Proper installation may cut energy costs by 10-30% and increase the longevity of air conditioning units by up to 10 years. Knowing the details of proper installation is essential for all, whether residential or commercial.
Benefits of Professional Installation
Poor installation results in inefficiency, higher energy bills, and system breakdowns. Optimal operation is guaranteed through professional installation in Palmdale, which caters to your unique needs. Engaging experienced professionals minimizes errors and enhances system reliability. Be it central air conditioning, ductless systems, or window units, professional guidance is crucial.
How We Install Your System
Our installation procedure consists of key stages that guarantee excellent results. We begin with a comprehensive evaluation of your needs and space. We offer advice on choosing the perfect system, then install it with precision. Typically, the steps are:
Step | Details |
---|---|
1. Preliminary Assessment | Determine your specific HVAC and AC needs |
2. System Selection | Pick the ideal HVAC system for your space |
3. Appointment Setting | Schedule the installation at your convenience |
4. Installation Process | Carefully and safely install the HVAC system |
5. System Testing | Conduct final tests to ensure peak performance |
6. Maintenance Guidance | Give guidance on proper system care |
Our detailed process ensures your HVAC system’s efficient operation for many years. In Palmdale, our emergency services deliver prompt, reliable solutions to restore comfort and security.
Fast and Trustworthy Repairs
Speedy and trustworthy repairs are essential for keeping your HVAC and air conditioning systems running smoothly. Unforeseen malfunctions call for prompt repairs. Skilled technicians in HVAC repair in Palmdale adeptly identify and fix these problems swiftly. This prevents minor issues from worsening into major complications.
Typical Issues in HVAC and AC Systems
Various problems can impair HVAC and AC units, such as:
- Thermostat malfunctions, leading to inconsistent indoor temperatures.
- Refrigerant loss that diminishes AC performance.
- Obstructed filters that decrease efficiency and raise costs.
- Insufficient airflow causing a decline in comfort.
- Unusual noises coming from the unit, indicating potential mechanical failure.
Proper AC repair in Palmdale addresses these issues. It enhances system performance and prolongs its durability.
How to Troubleshoot Minor Problems
Before contacting an expert in Palmdale, try these basic troubleshooting measures:
- Check the thermostat settings to ensure they are properly adjusted.
- Examine your filters and change them if they appear obstructed.
- Inspect the area around the unit for refrigerant leaks.
- Make sure that nothing is blocking the vents.
This early detection can prevent the need for urgent repairs, thereby saving on maintenance expenses.
Professional Installation Solutions
High-quality installation by professionals is essential. In Palmdale, Climate Control Heating, Cooling & Plumbing Inc. has over 36 years of experience delivering top-notch services. Their installations improve system efficiency and performance. Proper setup can reduce utility expenses by 10-30% and prolong the life of AC units by up to a decade. Grasping the ins and outs of installation is vital for both homeowners and businesses.
Why Professional Installation Matters
Improper installation can lead to reduced efficiency, increased costs, and frequent failures. Optimal operation is guaranteed through professional installation in Palmdale, which caters to your unique needs. Hiring seasoned technicians avoids common mistakes, boosting reliability and performance. Whether you need central AC, ductless mini-splits, or window units, expert consultation is essential.
How We Install Your System
We follow a detailed process to install your HVAC and AC systems flawlessly. It starts with an in-depth analysis of your area and requirements. We offer advice on choosing the perfect system, then install it with precision. Our process is structured as follows:
Step | Overview |
---|---|
1. Preliminary Assessment | Evaluate your system requirements and personal preferences |
2. System Selection | Choose the best unit for your environment |
3. Installation Scheduling | Arrange a suitable time for the setup |
4. System Installation | Carefully and safely install the HVAC system |
5. Completion Verification | Verify that the system operates flawlessly |
6. Maintenance Guidance | Give guidance on proper system care |
Our detailed process ensures your HVAC system’s efficient operation for many years. Our Emergency HVAC services in Palmdale provide quick, effective solutions when you need them most, guaranteeing your comfort and peace of mind.
Quick and Reliable Repairs
Quick and dependable fixes are crucial for HVAC and air conditioning systems to ensure home comfort. Unforeseen malfunctions call for prompt repairs. Proficient technicians in Palmdale are skilled at rapidly addressing and fixing problems. Such prompt action stops small problems from escalating.
Frequent Problems in HVAC and air conditioning Units
Frequent challenges encountered include:
- Thermostat issues resulting in uneven temperatures.
- Refrigerant leaks, which can compromise cooling efficiency.
- Dirty or blocked filters limiting airflow and driving up energy bills.
- Weak airflow, resulting in reduced comfort levels.
- Strange sounds emanating from the system that suggest mechanical issues.
Proper air conditioning repair in Palmdale addresses these issues. Such repairs boost performance and increase longevity.
Basic Troubleshooting Steps
Before contacting an expert in Palmdale, try these basic troubleshooting measures:
- Confirm the thermostat settings are appropriate.
- Examine your filters and change them if they appear obstructed.
- Look for any visible signs of refrigerant leaks around the unit.
- Make sure that nothing is blocking the vents.
This early detection can prevent the need for urgent repairs, thereby saving on maintenance expenses.
Quick and Reliable Repairs
If you’re searching for dependable HVAC and AC services in Palmdale, Fresh Air Conditioning and Heating is your trusted partner. We are renowned for our commitment to quality and customer satisfaction. We provide a range of tailored solutions to match each client’s specific requirements. Our focus on energy conservation and system reliability ensures you get the best service possible.
Our Commitment to Customer Satisfaction
We are recognized for our fast response times, critical in hot regions such as Palmdale. Our preventative maintenance plans are designed to avoid expensive failures and maintain efficiency in Palmdale. Our comprehensive warranty for AC installations offers peace of mind. We also offer duct renovation services to increase airflow and efficiency, which helps lower energy costs.
Customer Reviews
“The level of service from Fresh Air Conditioning and Heating is unparalleled. Their expertise in AC repair and commitment to energy-efficient solutions really made a difference in my home.”
“I appreciate the preventative maintenance plans offered. They keep my HVAC system running smoothly, helping me avoid unexpected repairs and additional costs.”
Service Offered | Details | Gains |
---|---|---|
Emergency AC Repair | Quick response to sudden system failures | Ensures comfort during hot periods |
Duct Renovation | Enhances airflow and improves indoor air quality | Reduces energy consumption and lowers bills |
Heating System Maintenance | Comprehensive services for various heating systems | Ensures optimal indoor comfort and efficiency |
Thermostat Upgrades | Implements smart technology for precise control | Enhances comfort and energy savings |
Contact Us Today for Affordable Solutions
When you need reliable HVAC and air conditioning services in Palmdale, Fresh Air Conditioning and Heating is the provider to call. Our team commits to affordable HVAC solutions that cater specifically to your needs. By contacting us, you gain access to a complimentary estimate. This enables you to assess different solutions without any commitment. Our priority is to maintain a comfortable environment for you. And, we aim for our services to efficiently and affordably meet your heating and cooling needs.
Get a Complimentary Quote
Whether you need a routine tune-up or a complete system replacement? getting in touch with an HVAC specialist in Palmdale is easy through us. With over 20 years of experience, our team ensures premium service with no hidden costs. We focus on transparency and your satisfaction. All key details are provided upfront. Contact us now for a no-cost estimate and see how we can enhance the comfort and efficiency of your home.
Get in Touch for Emergency Services
HVAC problems can emerge without warning. That’s why our crew is ready for emergencies anytime. From rapid repairs to comprehensive solutions, we are prepared to handle your emergency needs. Choose Fresh Air Conditioning and Heating in Palmdale as your reliable HVAC provider. We’re committed to ensuring your living space is comfortable with our dependable and reasonably priced HVAC offerings.
FAQ
What HVAC and AC services do you provide in Palmdale?
Our expertise covers HVAC installation, AC repairs, maintenance, and heating services to deliver year-long comfort.
How often should I schedule HVAC maintenance?
It is advisable to have your HVAC system serviced yearly. Consistent upkeep increases efficiency, lowers the risk of failures, and improves indoor air quality.
What are common signs that my HVAC system needs repair?
Look out for uneven temperatures, odd sounds, peculiar odors, rising energy expenses, and the system starting and stopping more often than usual. Observing these signs suggests a need for our repair services in Palmdale.
How can I select the right air conditioning system for my home?
Consider your home size, cooling demands, efficiency ratings, and budget when choosing an AC system. A correctly sized unit ensures maximum efficiency and comfort.
Why is professional HVAC installation important?
Substandard installation results in inefficiency, increased costs, and breakdowns. Therefore, hiring our experts ensures the best performance and longevity of your HVAC system.
What should I do if my air conditioner stops working?
First, check the thermostat, confirm the power supply, and examine the circuit breaker. Should the problem continue, call Fresh Air Conditioning and Heating in Palmdale for quick and reliable repairs.
How do I prepare my HVAC system for seasonal changes?
Prepare your HVAC system for seasonal changes by cleaning ducts, checking your furnace or AC, and scheduling regular maintenance. This approach prevents unexpected breakdowns during extreme weather.
Can you provide emergency HVAC services in Palmdale?
Indeed, Fresh Air Conditioning and Heating delivers emergency services for crucial heating and cooling situations. Our swift intervention helps restore your home’s comfort without delay.
What are the benefits of regular HVAC maintenance?
Regular HVAC maintenance not only prolongs system life but also enhances energy efficiency, reduces bills, prevents failures, and improves indoor air quality.
How can I get a free estimate for HVAC services?
Get in touch with Fresh Air Conditioning and Heating to receive a no-cost estimate. They will assess your needs and provide a tailored estimate for your HVAC requirements.
Select Fresh Air Conditioning and Heating in Palmdale for exceptional HVAC and air conditioning services that ensure comfort and energy savings. Benefit from a durable, efficient system by choosing our expert services today.